Offsite Construction 2024: Smart, Sustainable, and Efficient
The construction industry is undergoing a transformation, and at its forefront is offsite construction
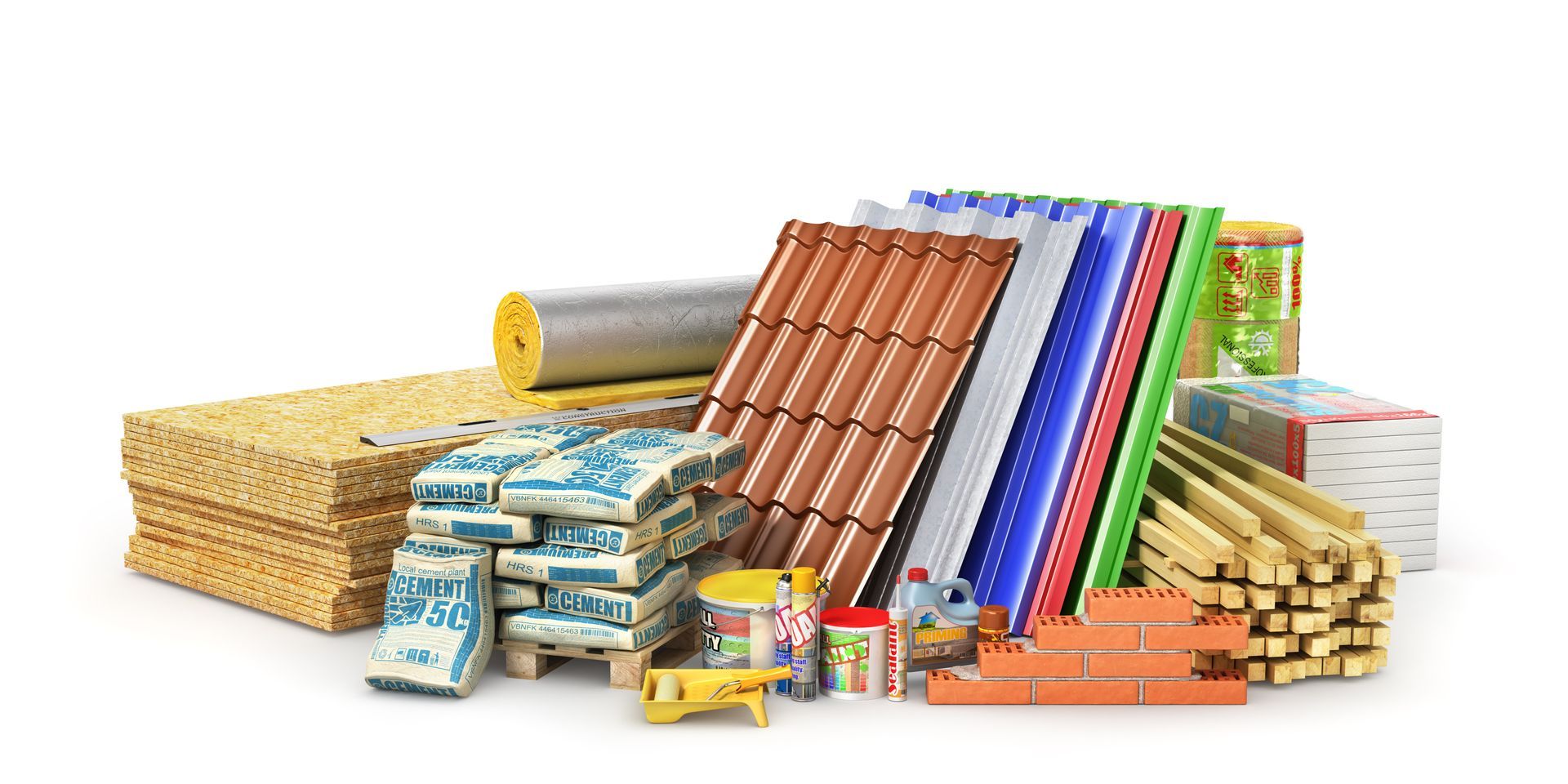
The construction industry is undergoing a transformation, and at its forefront is offsite construction. This alternative approach involves the assembly of building components or even entire structures in a controlled factory environment before transporting them to the construction site.
Offsite Construction
Offsite construction, often called modular or prefabricated construction, represents a considerable shift in the way we approach buildings. It reimagines construction as a manufacturing process, with building components being produced under controlled conditions in a factory. Once completed, these components are transported and swiftly assembled at the construction site. This approach offers numerous advantages over traditional onsite construction, with efficiency, quality, and sustainability being at the forefront.
Outlook
One of the most significant trends in offsite construction for 2024 is the rise of smart and sustainable solutions. Builders are increasingly incorporating cutting-edge technologies and sustainable materials into offsite construction processes. This not only enhances energy efficiency and environmental sustainability but also delivers structures that are smarter and more adaptive to the needs of occupants.
Another prominent trend is the growing acceptance and integration of offsite methods in urban development. As cities grapple with population growth, space constraints, and the need for rapid construction, offsite construction is seen as a viable solution. In 2024, more cities and developers are likely to adopt offsite techniques to meet housing demands, infrastructure needs, and other urban development challenges.
Collaboration and standardisation are also on the rise in offsite construction. Industry players are working together to develop common standards and best practices, reducing project risks, and ensuring quality control. This trend is expected to result in even more efficient, cost-effective, and high-quality construction processes.
Furthermore, as we head into 2024, offsite construction is breaking free from traditional building aesthetics. Architects and designers are embracing the flexibility offered by offsite methods to create unique, aesthetically pleasing structures that challenge conventional norms.
Building Materials for Offsite Construction
The choice of materials plays a pivotal role in ensuring the success of offsite construction projects. Among these materials, liquid screed is emerging as a valid solution, offering an array of benefits that bolster efficiency, quality, and sustainability in offsite construction.
Flooring is a crucial element in any building, and liquid screed plays a pivotal role in ensuring that floors are level, smooth, and structurally sound. Liquid screed is a self-levelling mixture that consists of cement, water, and additives. When applied correctly, it offers unmatched precision, reducing the need for manual levelling. Its rapid drying time also accelerates construction schedules, making it an ideal choice for offsite projects.
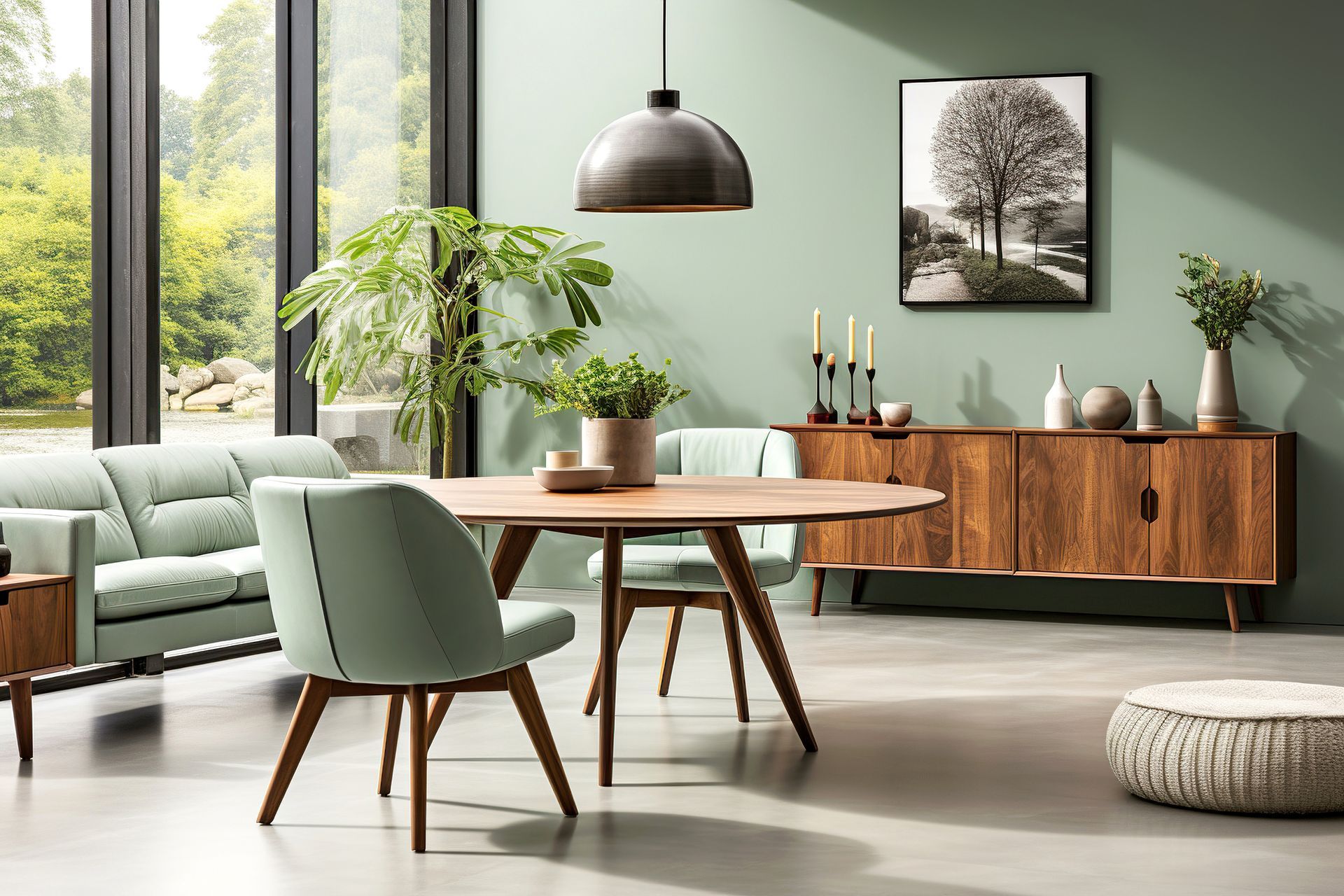
Liquid Screed in Offsite Construction
Efficient: Clean and No Waste
- Clockwork Screed has innovative mobile trucks that batch-produce the liquid screed on the truck and pump it in high volumes directly onto the floor surface where it is required. Around 1000m² of floor can be covered in one day. On average, a job is completed within 4-5 hours. By comparison, a traditional floor screed is brought to site in a truck mixer for another contractor to pump, level and finish the screed, or the screed is wheelbarrowed to the room and manually applied. Time-consuming, labour-intensive and messy the job can take up to a week to be completed.
Reduced On-Site Labour:
- The consistency achieved with liquid screed is difficult to replicate with traditional screed, which often relies on manual labour for spreading and levelling. Poured liquid screed doesn’t require manual ‘levelling’.
Accelerated Schedules:
- Liquid screed dries considerably faster than traditional screed, enabling quicker turnaround times in construction schedules. This acceleration benefits project stakeholders by allowing for faster occupancy or rental income generation.
Quality Assurance and Sustainability
Quality control is central to offsite construction, and liquid screed enhances it in multiple ways:
Superior Finish:
- Liquid screed creates a smooth, level surface that consistently meets stringent quality standards, ensuring precision and excellence throughout the project.
Reduced Cracking:
- Liquid screed is less prone to cracking compared to traditional screed, a vital characteristic in buildings subject to heavy loads or temperature fluctuations.
Sustainability Goals:
- Sustainability is a top priority in today's construction industry. Liquid screed aligns seamlessly with these goals, including its compatibility with underfloor heating systems, which enhances the thermal performance of offsite constructions and contributes to energy-efficient buildings.
Offsite construction is increasing in popularity in construction, because of its precision, quality, and sustainability benefits. While the spotlight may not always be on the materials used, they play an integral role in realising the full potential of this transformative approach. Liquid screed, with its adaptability, efficiency, quality assurance, and sustainability benefits, is an important element that ensures the success of offsite construction projects, contributing to a more efficient, cost-effective, and environmentally conscious built environment.
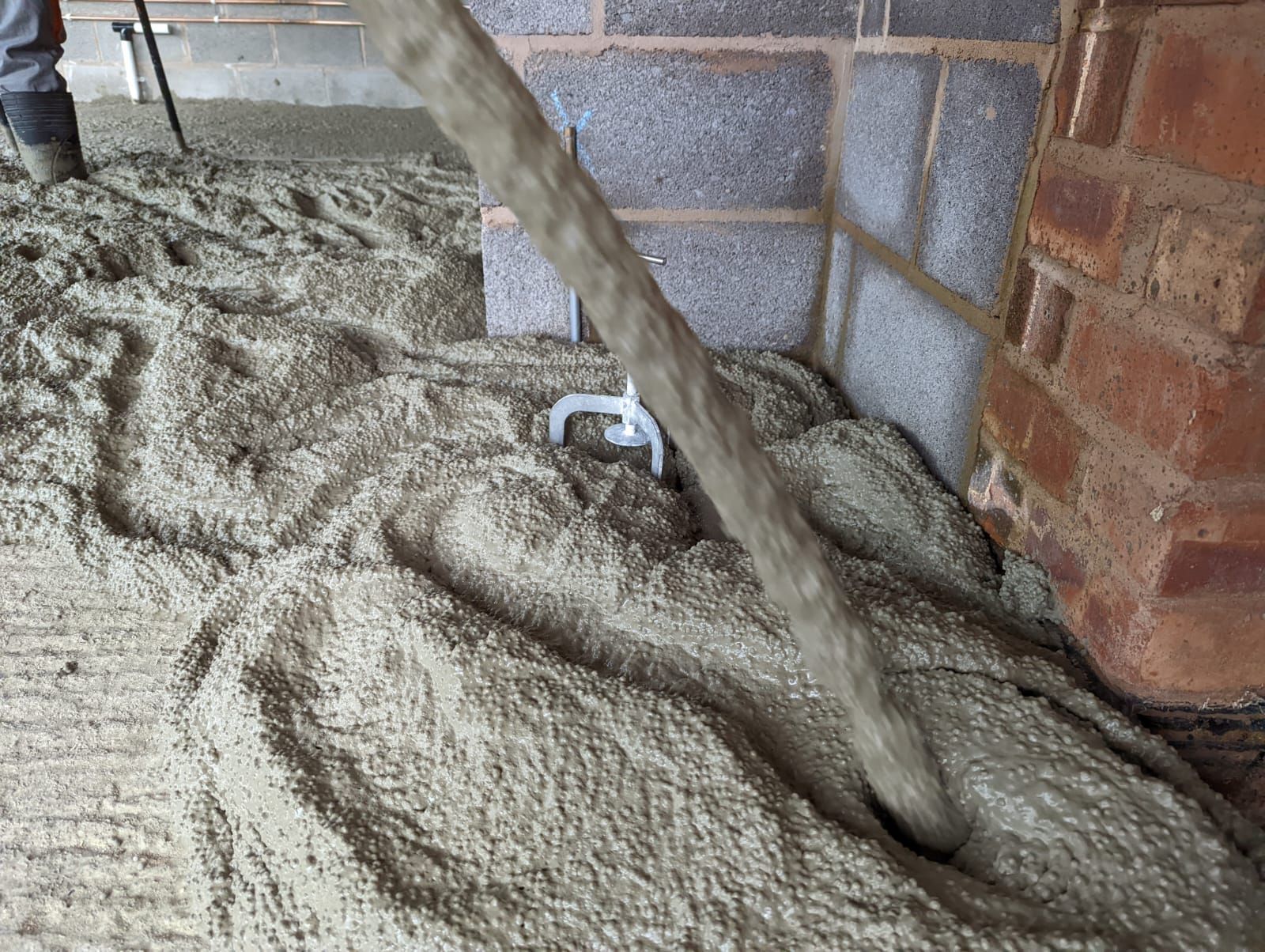
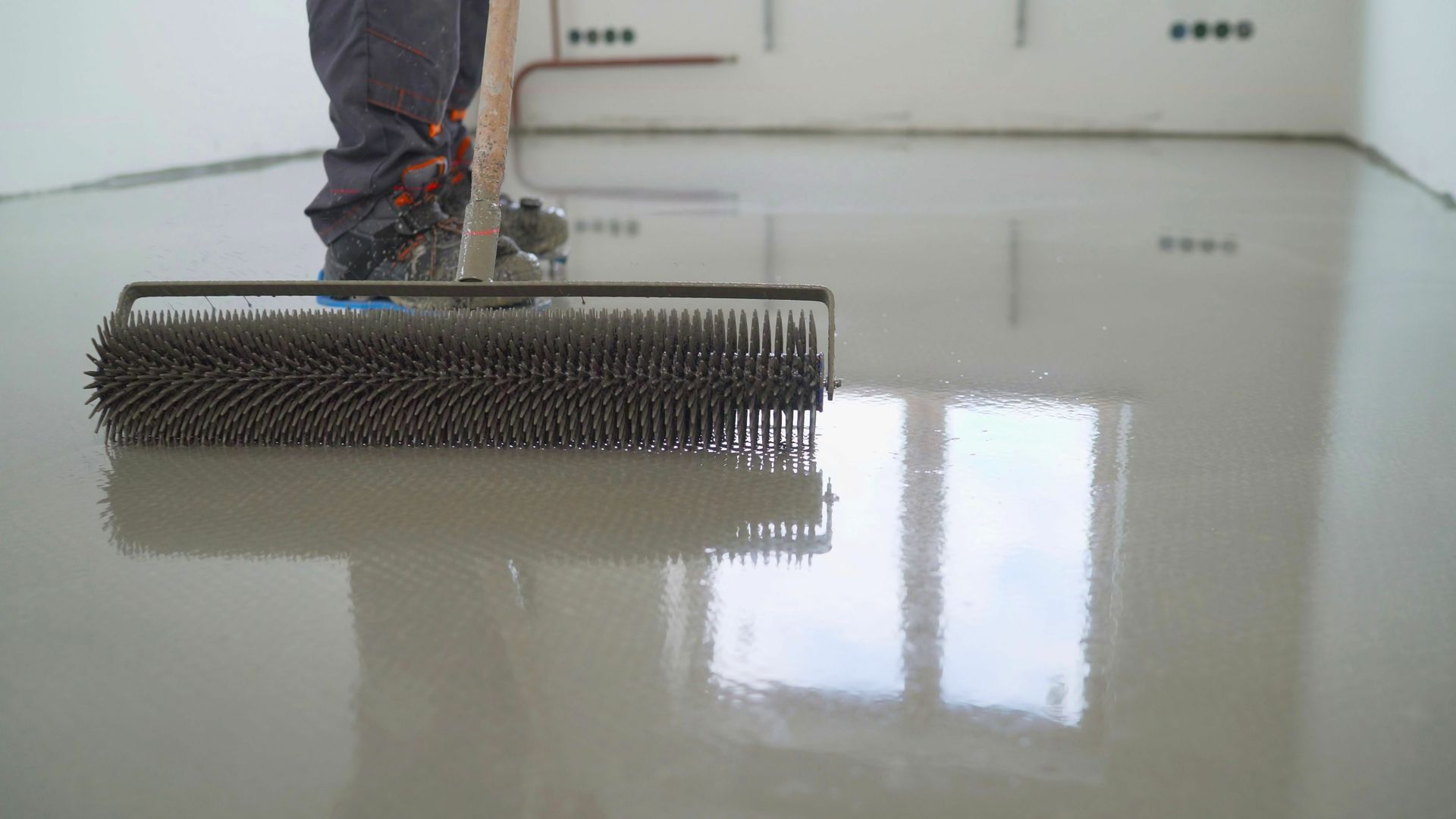