Liquid floor screed drying times
Liquid floor screed drying times are an important consideration for any contractor or home owner. The type of liquid screed used in an installation will affect the time it takes to dry, ready for the floor finish to be laid.
Screed flooring should be allowed to dry slowly (or cure). This is because the screed needs to retain its moisture for as long as possible to avoid the cracks that can occur when dried rapidly.
To help draw out the process, a polythene sheet can be used to cover the screed for several days.
Liquid screeds like those supplied by Clockwork Screed, take considerably less time to dry because they’re not as thick and they also have better drying properties. They can even be dried using dehumidifiers. This is the advantage of using liquid screeds over hand-mixed.
Three main types of floor screeding we will focus on and their drying times, include traditional sand and cement screed, anhydrite screed, and cement based liquid screed (often known as cementitious screed).
Types of floor screed
Traditional sand and cement screed
Traditional sand and cement screed is a time-tested solution that has been around for many years, and consists of a mix of sand, cement, and water. Once mixed, it is applied manually and requires skilled labour to ensure an even surface across a floor covering.
It provides a robust and durable flooring option, however due to the manual nature of installation the process can lead to inconsistencies in level and finish if not done by experienced professionals.
Anhydrite screed
Anhydrite screed is a gypsum-based liquid screed that is pumped onto the floor area, offering a faster and more efficient installation process than traditional sand and cement screed.
It is good choice for underfloor heating systems due to its thermal conductivity. However the gypsum content can be susceptible to moisture meaning it isn’t suitable for applications in bathrooms or wetrooms.
Cement based screed (cementitious screed)
Cement based liquid screed is a self-levelling screed that combines the benefits of traditional screed with the ease of application of liquid screeds. It offers excellent durability and is suitable for both residential and commercial applications.
It is compatible with underfloor heating, providing good thermal conductivity and faster heat response times. Its formula means it benefits from reduced drying times compared to traditional sand and cement screed, allowing for quicker access to the floor for subsequent trades.
The self-levelling property ensures a high-quality, smooth, and level finish with minimal effort from the installer. It offers a high strength and resistance to cracking, providing a durable and long-lasting flooring solution.
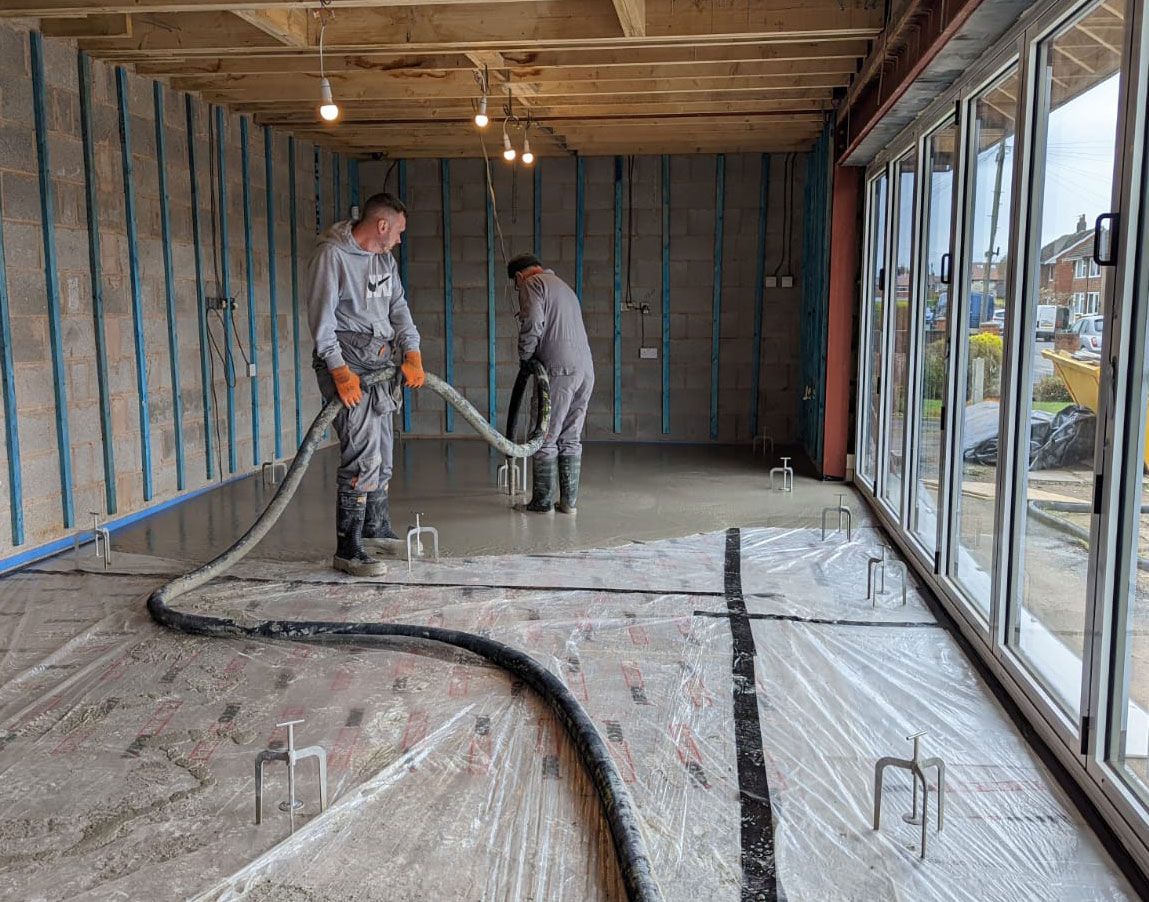
Initial setting time
Traditional sand and cement screed
The setting time for traditional sand and cement screed can vary, but it generally starts to set within 24 to 48 hours under optimal conditions.
However, it is important to note that while it may start to harden, the screed isn't fully cured and able to bear loads until much later.
Anhydrite screed
Anhydrite screed typically starts to set within 24 to 48 hours as well, and similar with the traditional sand and cement screed, the surface is not ready for light foot traffic or further work until a few days after pouring.
The complete drying time before final floor coverings can be laid depends on the thickness and environmental conditions but generally requires several weeks to fully dry and cure.
Cement based screed (cementitious screed)
Cement-based liquid screeds usually have a faster initial setting time compared to anhydrite screeds, often beginning to set within a few hours after application.
They can typically accept light foot traffic within 24 to 48 hours. However, the complete cure time, which is necessary before applying final floor finishes, still depends on the thickness of the screed and environmental conditions.
Complete dry and curing times
Traditional sand and cement screed
For a traditional sand and cement screed, the rule of thumb is a drying time of approximately 1 mm per day up to 40 mm thickness, and then it slows to 0.5 mm per day for thicknesses beyond 40 mm.
For full curing and to reach its optimal strength, it typically requires around 28 days under ideal conditions.
However, it is crucial to ensure that the moisture content meets the requirements for the final floor covering, which might necessitate additional drying time.
Anhydrite screed
Anhydrite screeds generally dry at a rate of 1 week per 10 mm of screed thickness, but it requires at least 28 days to cure fully before any final floor finishes are applied. The actual drying time can be longer depending on the environmental conditions and the screed's thickness.
The screed must also be sanded to remove the laitance (a weak, crumbly layer on the surface) before applying floor finishes.
Cement based screed (cementitious screed)
Cement-based liquid screeds can dry and cure faster than anhydrite screeds, with light foot traffic possible in 24 to 48 hours after application.
The drying time before applying final floor coverings is approximately 28 days under optimal conditions, but this can vary depending on the screed's depth and environmental factors.
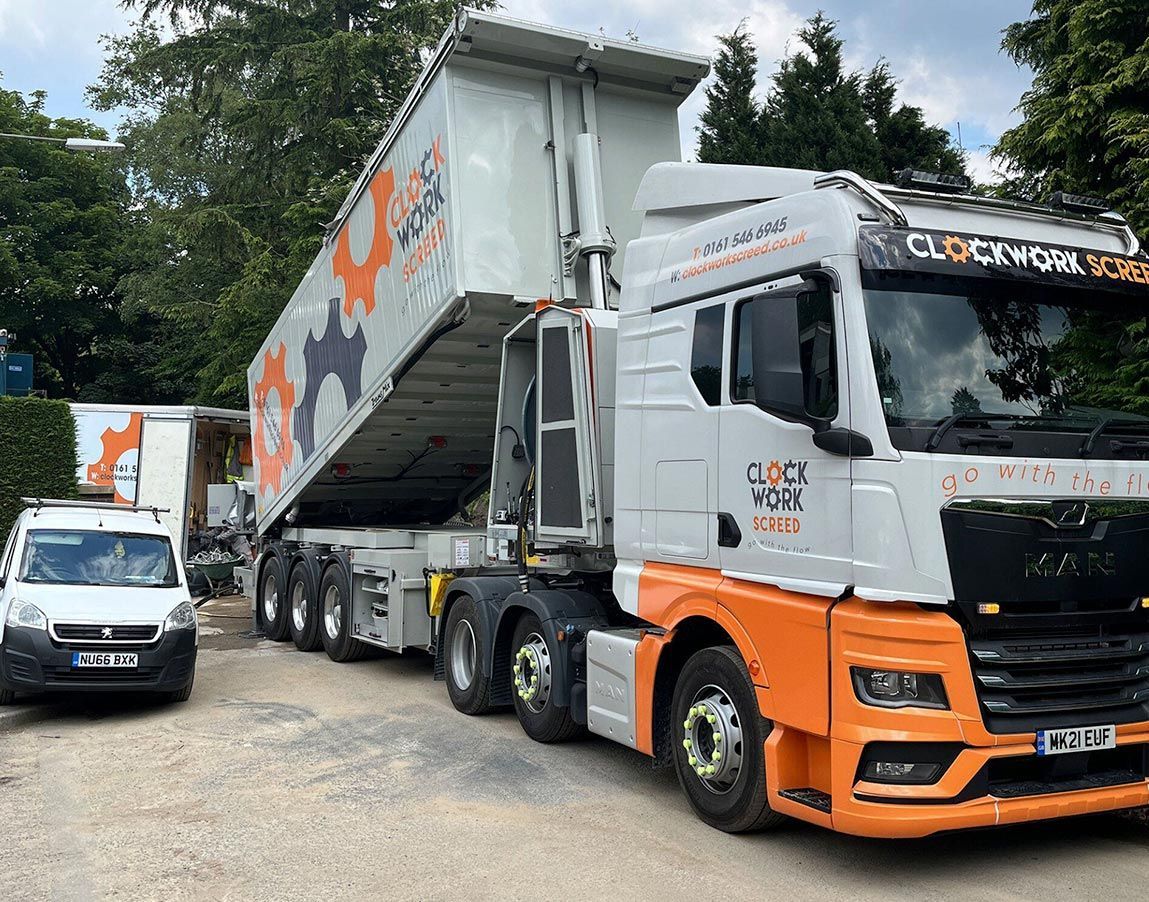
Environmental considerations
Traditional sand and cement screed
Traditional sand and cement screed uses a significant amount of cement, which has a high carbon footprint due to the energy-intensive production process.
Also, when used in conjunction with underfloor heating, sand and cement screed can be less efficient than liquid screeds due to its lower thermal conductivity. This means it may require more energy to heat a space effectively.
Anhydrite screed
Anhydrite screed is made from a by-product of the chemical industry (gypsum) which reduces energy during production and also contributes positively to the circular economy.
Anhydrite screed has good thermal conductivity, making it more efficient for use with underfloor heating systems compared to traditional screed. This can lead to lower energy usage over the lifetime of the flooring.
Cement based screed (cementitious screed)
Cement-based liquid screeds offer excellent thermal conductivity, making them efficient for use with underfloor heating systems and potentially reducing energy consumption for heating.
Unlike anhydrite screeds, there is no surface laitance (or dust) after curing and the floor will be compatible with all cement-based adhesives including fast-track systems.
The choice of screed can influence the overall environmental footprint of a building project. Therefore, when selecting a screed, it's beneficial to look for options that offer reduced carbon footprints, compatibility with energy-efficient heating systems.
Selecting the right Screed for your project
FAQS
What is liquid floor screed, and how does it differ from traditional screeds?
Liquid floor screed is a self-compacting material poured directly into place. It has few advantages such as faster installation, improved floor flatness, and compatibility with underfloor heating systems.
Traditional screeds, like sand and cement, are manually applied and prone to cracking and shrinking.
How long does it take for liquid floor screed to dry?
Clockwork Screed’s cementitious liquid screed typically dries within 24-48 hours for initial setting and 14-21 days for full readiness for top floor application. However, drying times can vary based on factors like temperature, humidity, and screed thickness.
What are the different types of floor screeds available?
The main types of floor screed during construction include traditional sand and cement, anhydrite screed, and cement based screed (sometimes known as cementitious screed).
How do environmental factors affect the drying time of liquid floor screed?
Environmental factors such as temperature, humidity, and airflow directly impact the drying process of liquid floor screed. Warmer temperatures and lower humidity levels generally lead to faster drying times, while adequate airflow is essential for promoting moisture evaporation.
How should liquid floor screed be cured and dried properly?
Proper curing and drying of liquid floor screed involve providing the right amount of moisture, temperature, and time for the flooring to develop its necessary properties.